High temperature compression springs are essential components in applications where resilience and stability are tested by extreme heat and they are increasingly vital across industries such as aviation, automotive, and manufacturing. Their versatility and durability represent both engineering challenges and feats of innovation.
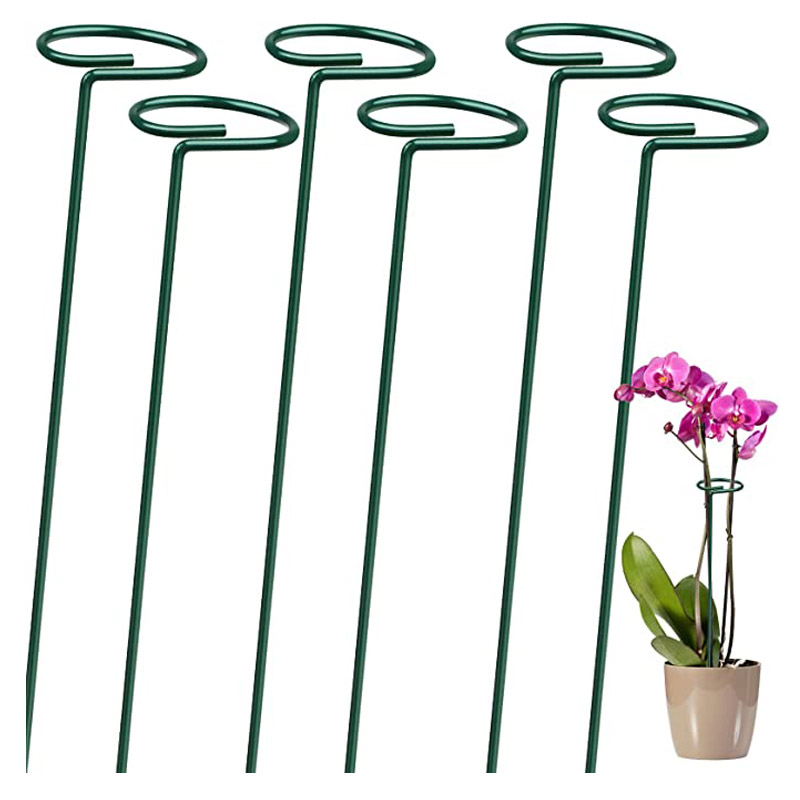
Compression springs are fundamental mechanical devices designed to absorb and store energy by resisting compressive forces. However, the capability to efficiently operate in high-temperature environments is what differentiates high temperature compression springs from standard ones. This unique attribute makes them indispensable in industrial scenarios where standard springs would fail due to heat stress.
In high-temperature applications, the functionality of these springs is critically dependent on the materials used. High-grade alloys such as Inconel, Nimonic, and stainless steel are commonly deployed due to their superior heat resistance and ability to maintain performance at elevated temperatures. Inconel, for instance, retains its resilience even when temperatures soar beyond 1000°F, ensuring the springs' structural integrity remains uncompromised.
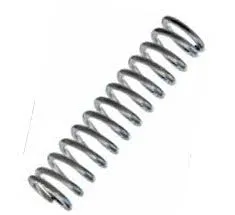
Material science is just one part of the equation; the design and manufacturing precision also play pivotal roles in the effectiveness of high temperature compression springs. Advanced computational tools and simulations are employed to optimize spring design, reducing material waste while maximizing performance. This precise engineering ensures that each spring can handle specified operational loads without succumbing to creep or fatigue, which are common failure modes in high-temperature environments.
Furthermore, industry standards and regulations underscore the critical nature of quality assurances in manufacturing these springs. Compliance with standards such as ASTM A354 for mechanical properties or ISO 9001 for quality management systems reinforces the springs’ reliability and suitability for high-stakes applications.
In practice, the adoption of high temperature compression springs is as varied as it is widespread. In aerospace, they are utilized within jet engines and landing gear assemblies, components where thermal stress is a constant challenge. The springs ensure mechanical systems respond predictably, maintaining safety and performance even in extreme conditions. The automotive sector also heavily relies on these springs for exhaust systems, turbochargers, and engine components, where heat dissipation is a critical concern.
high temperature compression springs
Manufacturers relying on high temperature compression springs must also invest in rigorous testing and quality control measures to guarantee longevity and performance. This includes thermal cycling tests, fatigue testing, and relaxation tests at the extremes of operating temperatures. By verifying these parameters, manufacturers not only uphold the springs’ performance but also fortify trust among their clientele.
On the frontier of innovation, research is channeling focus towards enhancing service life and efficiency. Developments in nanocomposite coatings and heat-resistant treatments promise to extend the operational lifespan and performance of these springs beyond what current technology can offer. Continued collaboration between industry and academia is driving breakthroughs that push boundary limits of temperature resilience.
Understanding the lifecycle of high temperature compression springs further cements their importance. Maintenance and regular inspection are crucial and often necessitate specialized knowledge to anticipate and mitigate potential failures. Experienced technicians are invaluable in assessing wear and potential points of failure, ensuring timely replacements or refinements to avert operational disruptions.
For businesses integrating these devices into their operations, choosing a supplier with a proven track record of expertise in high-temperature applications is paramount. Suppliers should not only provide high-quality products but also offer technical support, and insights into optimal application strategies. This fosters a collaborative relationship that maximizes system efficiencies, prolongs equipment longevity, and ultimately, reduces costly downtimes.
As industries inevitably stretch the limits of what can be achieved at high temperatures, the role of high temperature compression springs will inevitably grow. Their ability to translate intricate engineering into everyday applications stands as a testament to their indispensable nature. It’s more than just a mechanical device; it's a critical enabler of high-performance, high-temperature operations. As technology evolves, so too will these springs, maintaining their status as essential engineering solutions across the globe.