Welding coil springs is a task that requires precision and expertise to ensure proper functionality and safety. Coil springs are critical components in various applications, especially in automotive suspensions, where they absorb shocks, maintain vehicles' height, and ensure a smooth ride. Their integrity directly affects performance, making robust welding processes indispensable.
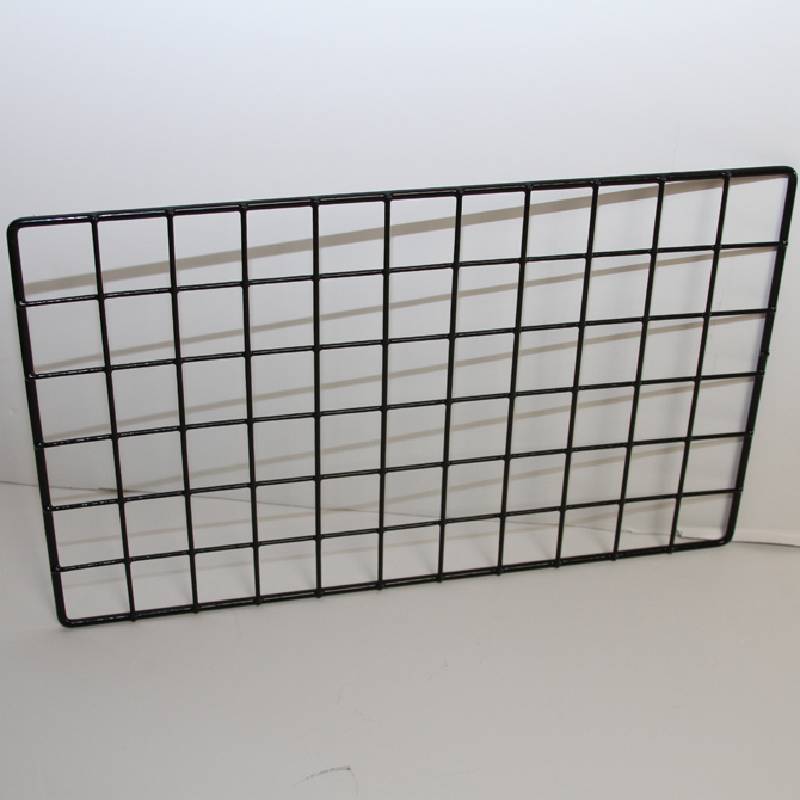
Understanding Coil Springs Coil springs, typically made from high-strength steel, are helical structures designed to compress and extend as loads are applied. This repetitive stress calls for welds that can withstand significant forces without failure. Each weld must maintain the spring's original properties, ensuring it doesn't weaken the steel or alter its stress distribution.
Welding Techniques Selecting the right welding technique is crucial for coil springs. Gas Metal Arc Welding (GMAW/MIG) and Gas Tungsten Arc Welding (GTAW/TIG) are often preferred. GMAW provides good penetration and a relatively fast welding speed, essential for larger manufacturing runs. Conversely, GTAW allows for precise control necessary for ensuring uniform welds without compromising structural integrity.
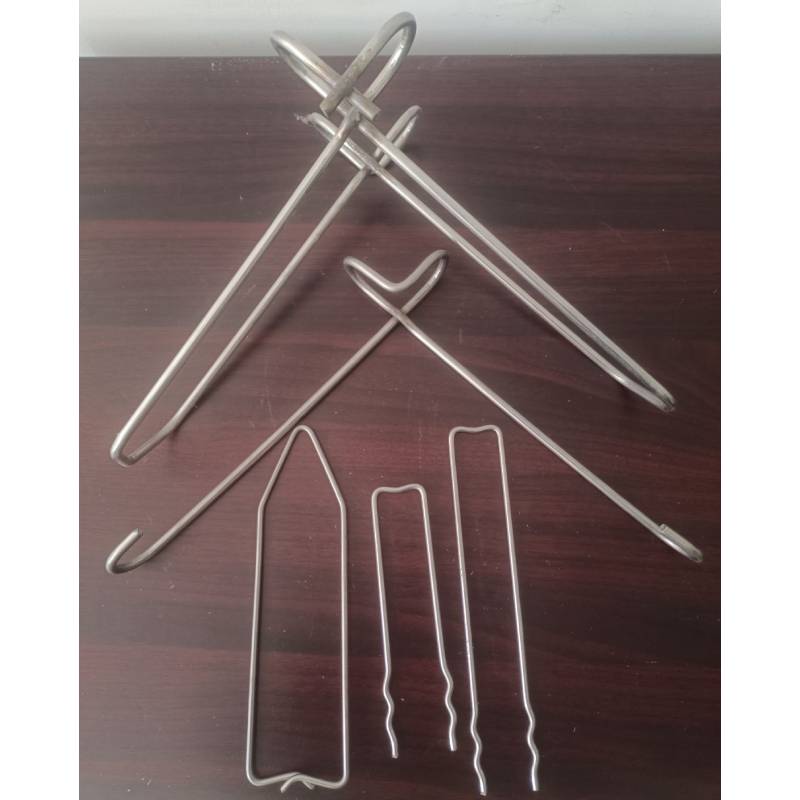
The Art of Temperature Control Managing heat input is perhaps the most significant challenge in welding coil springs. Excessive heat can alter the spring's properties, leading to reduced elasticity or even premature failure. It's paramount to keep the heat-affected zone (HAZ) minimal. Using techniques such as pulse welding can help control temperature, providing a strong bond while maintaining the metal's characteristics.
Material Compatibility Not all steels are created equal, and when welding coil springs, one must consider the specific alloy in use. Many coil springs employ alloy steel for added strength. Understanding the specific grade and its properties, such as carbon content and alloying elements, ensures the welding process aligns with the metal's characteristics, avoiding adverse effects like brittleness or corrosion.
welding coil springs
Post-Weld Heat Treatment Heat treatments post-welding can relieve stresses induced during the process, refining the grain structure and restoring the metal’s original strength. Annealing or tempering, depending on the initial material and application, can help in regaining the required mechanical properties. This step is crucial in high-performance settings such as automotive or industrial machinery, where springs repeatedly endure extreme conditions.
Importance of Quality Assurance Welding coil springs necessitates rigorous quality control measures. Non-destructive testing (NDT) methods like ultrasonic testing or magnetic particle inspection can identify potential defects. These tests assure the welds maintain the necessary standards, providing confidence that the springs will perform under expected loads.
Industry Standards and Compliance Adhering to established standards such as those from the American Welding Society (AWS) or equivalents in other regions underpins trustworthiness and reliability. Compliance ensures welds meet industry benchmarks for safety and performance, essential for manufacturers whose products often undergo stringent scrutiny.
Continual Advancements The field of welding, especially in coil springs, is ever-evolving. Emerging technologies like robotic welding and advancements in metallurgical science continually push the envelope, offering new methods to enhance weld quality and efficiency. Staying abreast of these developments, investing in training, and adopting innovative techniques is key for any manufacturer aspiring to lead in this domain.
Welding coil springs combines art, science, and craftsmanship. By prioritizing precision, understanding material science, and adhering to rigorous standards, one can achieve welds that ensure safety, performance, and reliability. The pursuit of expertise, trustworthiness, and authoritative methodologies remains integral in manufacturing strong and durable coil spring systems, offering assurance to users across the globe.