When it comes to enhancing the durability and strength of concrete structures, welded wire mesh emerges as a pivotal component. This mesh, a grid formed by welding transverse and longitudinal steel wires at their intersections, plays a significant role in various construction projects, offering a blend of expertise and trustworthiness in its application.
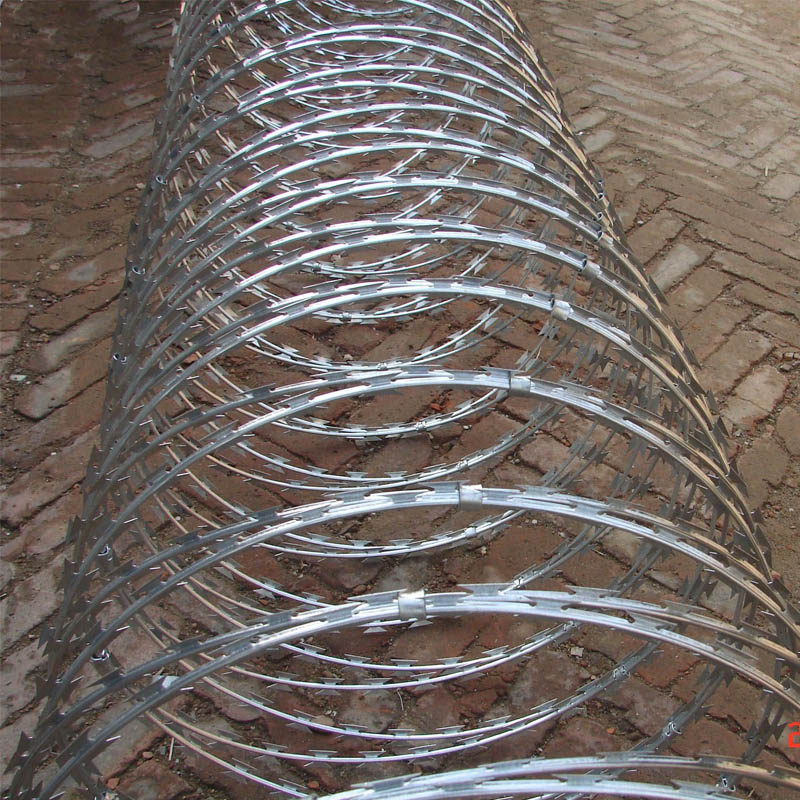
One of the critical experiences in using welded wire mesh for concrete is its remarkable ability to distribute loads across a broader area, which mitigates the risks of cracking and enhances structural integrity. Professionals in construction often prefer this mesh because of its ease of installation. Unlike traditional rebar, which demands meticulous placement and tying, welded wire mesh can be laid out swiftly, ensuring that large areas are uniformly reinforced. This not only saves time but reduces labor costs, which is paramount in large-scale projects.
From an expertise standpoint, welded wire mesh can significantly improve the tensile strength of concrete. It serves as a skeletal framework, providing the necessary tension support that complements the compressive nature of concrete. This is particularly important in applications like slabs, walls, and pavements, where tensile forces can compromise structural integrity. The mesh’s uniform grid pattern also ensures that shrinkage stresses are evenly distributed, thus preventing the formation of unwanted fractures.
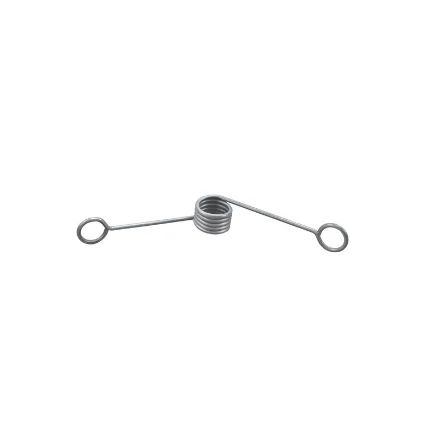
In terms of authoritativeness, welded wire mesh is recognized internationally as a standard in construction reinforcement. Specifications for these meshes are detailed in building codes and industry standards, reflecting global consensus on their utility and effectiveness. This authoritative backing ensures that using welded wire mesh is not merely a trend but a validated practice endorsed by engineering professionals and governing bodies alike.
Trustworthiness in construction materials is paramount, especially concerning safety and longevity. Welded wire mesh is manufactured using high-quality steel that adheres to stringent industry standards. This guarantees not only the mesh’s strength and flexibility but its resilience to adverse conditions such as corrosion and mechanical stress. Moreover, the welding process ensures that every joint is robust, minimizing the chances of failure even under significant pressure or environmental challenges.
welded wire mesh for concrete
Another key aspect of welded wire mesh is its adaptability to various construction needs. Available in a range of sizes and wire diameters, it can be custom-tailored to specific project requirements. This flexibility makes it a go-to choice for architects and engineers who need a reliable reinforcement solution that can be seamlessly integrated into different design paradigms.
Using welded wire mesh also exemplifies a commitment to eco-friendly construction practices. The production processes are generally less energy-intensive compared to other reinforcement options, and the materials are often recyclable. This environmental consideration is becoming increasingly relevant as industries worldwide strive to reduce their carbon footprints and promote sustainable building practices.
Contractors and builders who incorporate welded wire mesh into their projects frequently report improved project timelines and enhanced structural performance. Real-world applications consistently demonstrate the mesh’s capacity to maintain its integrity over extended periods, even in challenging environments. For instance, in infrastructure projects like bridges or roadways, where durability and reliability are non-negotiable, welded wire mesh consistently proves its worth.
In conclusion, welded wire mesh is not just an accessory in concrete reinforcement; it is a foundation for dependable and robust construction. Its benefits, backed by substantial professional experience, authoritative standards, and eco-friendly properties, position it as an indispensable tool in modern civil engineering. As construction demands evolve, the role of welded wire mesh will undoubtedly expand, continuing to build trust and setting benchmarks in quality and safety across the industry.