Understanding the intricacies of construction materials is pivotal for project efficiency and cost management. Concrete mesh, an essential reinforcement component in construction, plays a significant role in the stability and longevity of concrete structures. This article delves into the cost factors, practical experiences, and critical insights around concrete mesh, tailored to enhance understanding and optimize purchasing decisions.
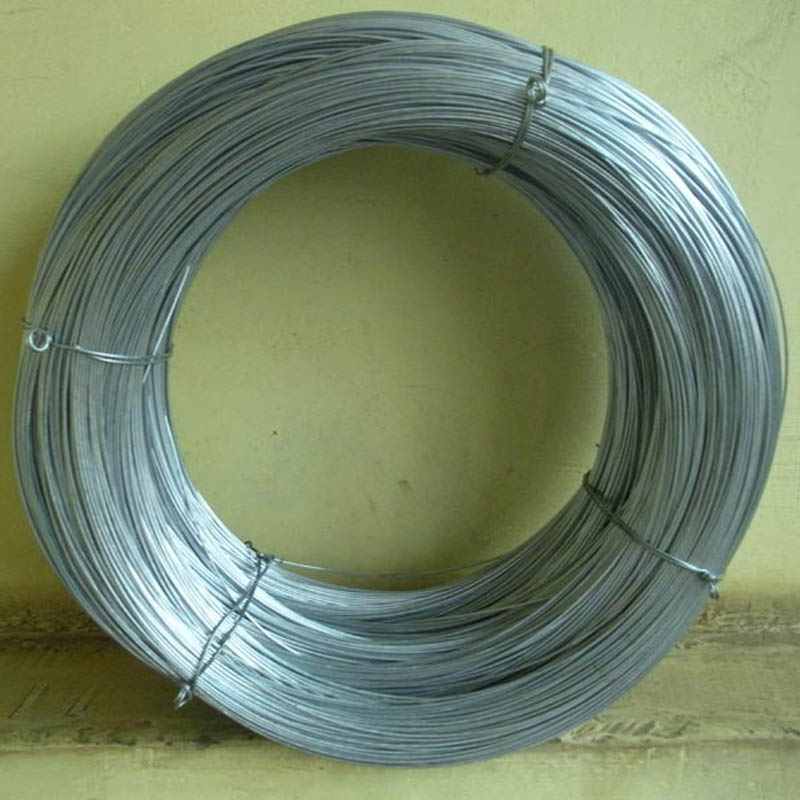
Concrete mesh, commonly made of steel, serves as an reinforcing agent that ensures even distribution of tension across the surface of a concrete slab, reducing the risk of cracks and structural weaknesses. This reinforcement is critical in applications ranging from residential driveways to commercial foundations. However, determining the cost of concrete mesh involves several variables, each influencing the final expenditure.
Firstly, material quality is a primary determinant of cost. High-grade steel, often galvanized for rust resistance, typically commands a higher price due to its durability and extended lifespan. Conversely, non-galvanized or low-grade steel may present initial savings, but its susceptibility to corrosion can lead to increased maintenance costs and reduced overall structural integrity. Therefore, it is advisable to weigh initial material costs against potential long-term benefits and expenses.
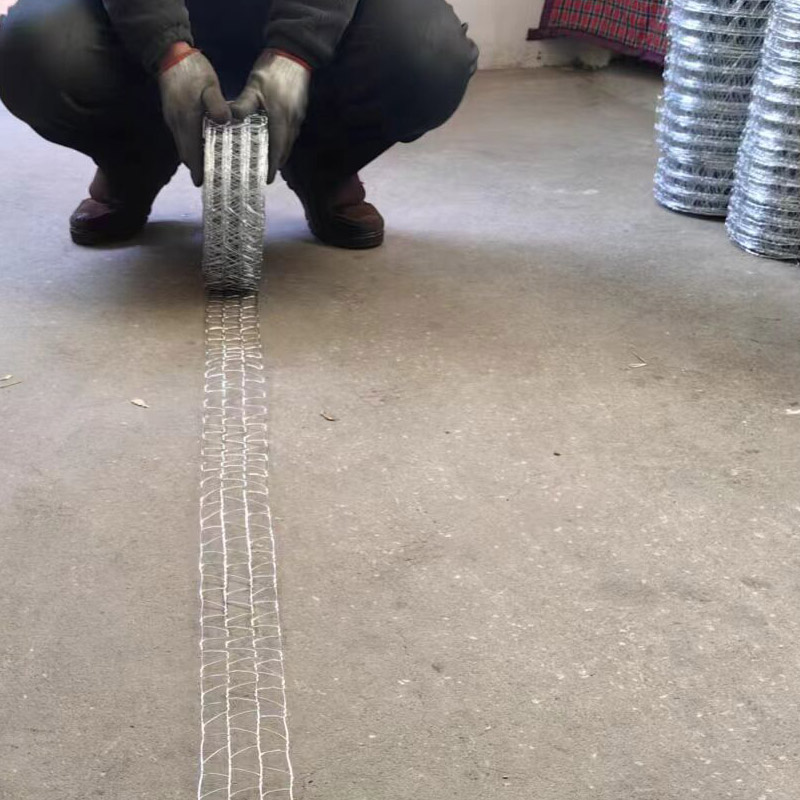
Mesh size and gauge are also significant factors impacting cost. Mesh with smaller openings and thicker wires generally costs more because it requires more material, offering enhanced strength and support. For heavy-duty construction works, such as industrial floors or highway paving, investing in denser mesh can prevent costly repairs or replacements down the line.
Installation complexity is another cost component. Basic projects with straightforward layouts might incur minimal installation fees, whereas intricate designs or large-scale projects can escalate labor charges substantially. Experienced contractors may charge higher rates, but their expertise ensures that the mesh is installed efficiently and correctly, minimizing the risk of errors and subsequent costs.
concrete mesh cost
For accurate budgeting, consider the project’s specific requirements.
Quantity impacts total expenditure; buying in bulk often reduces the per-unit cost. However, overbuying due to poor planning can lead to unnecessary expenses, particularly if excess material cannot be returned. Engaging with suppliers for bulk discounts or return policies can offer economic advantages.
Furthermore, geographical factors can affect mesh pricing. Areas with limited access to quality materials may face inflated prices due to transportation costs and supply constraints. Conversely, regions with a competitive market for construction supplies might offer more favorable pricing through increased supplier competition.
Experience in sourcing and negotiating can significantly impact overall costs. Knowledgeable procurement teams or contractors can identify cost-saving opportunities such as end-of-season sales, promotional discounts, or alternate suppliers. Their expertise allows for strategic purchasing decisions that align best with budgetary constraints without compromising quality.
The reliability and trustworthiness of suppliers should not be overlooked. Reputable suppliers often provide material certifications, ensuring authenticity and compliance with industry standards, which is crucial for maintaining structural safety and meeting regulatory requirements. Supplier credibility can safeguard against counterfeit or substandard materials that jeopardize project integrity.
In conclusion, while the initial cost of concrete mesh is a crucial consideration, understanding the broader context of its application, quality, installation, and supplier reliability can lead to more informed decisions. By evaluating these factors critically, one can achieve a balance between cost efficiency and quality performance, ultimately ensuring the success and durability of construction endeavors. As such, concrete mesh should not merely be viewed as an expense but as a vital investment in the long-term resilience and safety of the built environment.