Unlocking the Potential of Spring for Wire Solutions
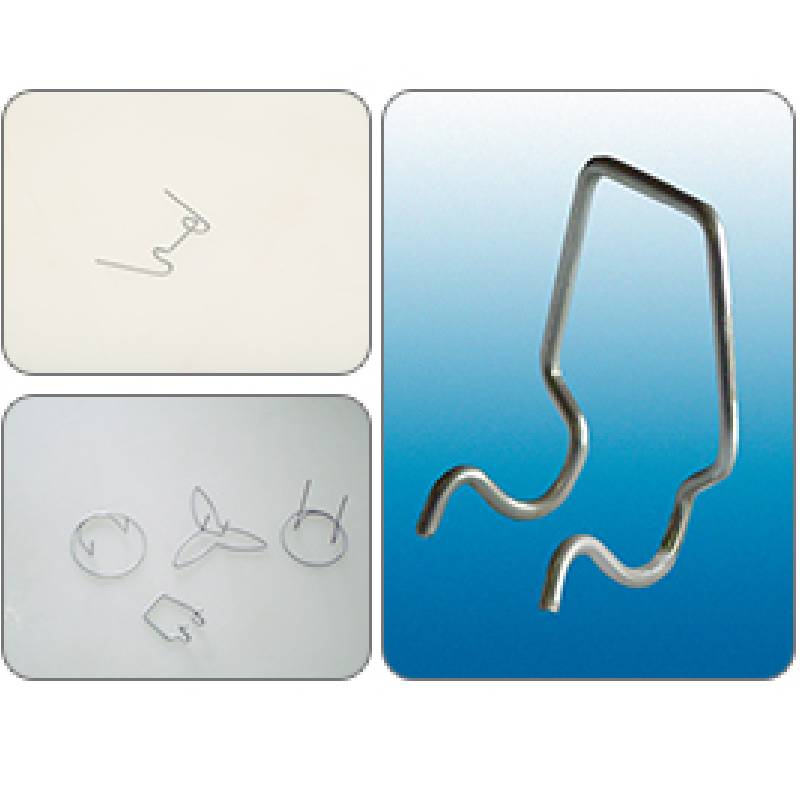
The world of wire manufacturing is intricate, demanding precision and expertise to ensure the highest quality outcomes. At the heart of this realm lies the often-overlooked yet vital component the spring. This deceptively simple device plays a crucial role in a variety of wire applications, from industrial machinery to consumer electronics. Understanding how to optimize the use of springs in wire manufacturing can drive significant improvements in product durability and performance, thereby enhancing customer satisfaction and boosting market competitiveness.
Springs, in essence, are the unsung heroes in wire applications. They provide tension, absorb shocks, and offer support, all critical for a myriad of applications. Their main function is to store mechanical energy and release it when needed, a principle that has facilitated innovation across industries.
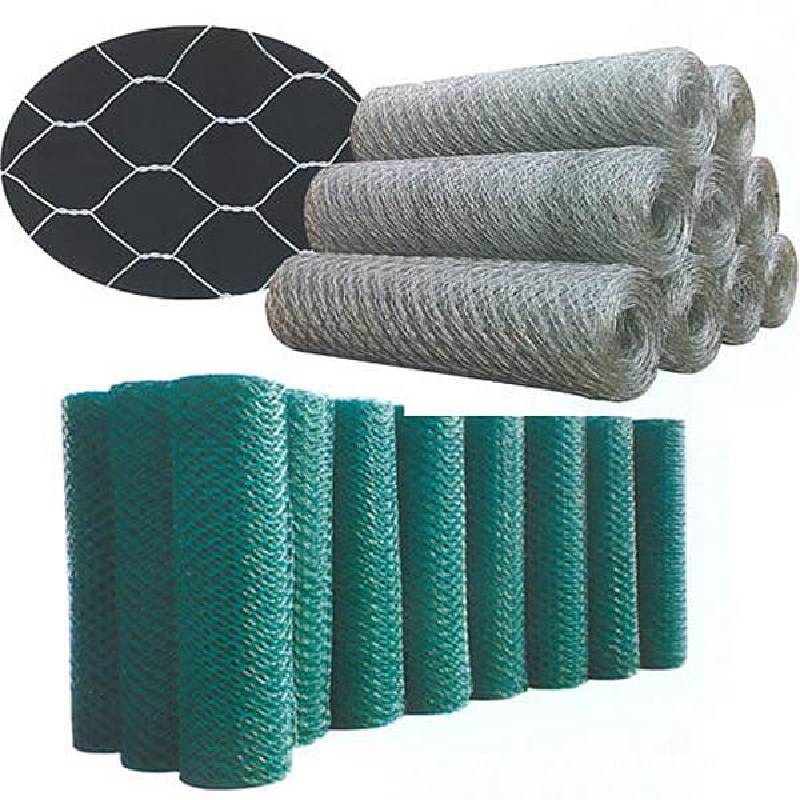
The creation of springs for wire begins with material selection. High-carbon steel, stainless steel, and other alloys are common choices due to their flexibility and strength. While material selection might appear straightforward, achieving the right balance of properties requires expertise. For example, the type of alloy used can significantly influence the spring's resilience and ability to withstand environmental stresses like corrosion or fatigue.
The next crucial stage is the manufacturing process, which involves forming, heat-treating, and finishing. Forming involves coiling the wire into a helical or other shapes, a stage that demands precision to prevent defects. Heat treatment enhances the material’s mechanical properties, such as strength and elasticity, enabling the spring to retain its shape and perform effectively under repeated stress. Finishing techniques, such as shot peening or coating, further bolster the spring's durability and resistance to wear and tear.
What sets spring manufacturing apart is the expertise required to customize springs according to specific applications. This customization can include variations in size, tension, and design. For wire-based applications, the spring's tension must align perfectly with the wire’s properties and the intended use. An incorrect tension rating can lead to premature failure or suboptimal performance. Moreover, customizing a spring for a sophisticated application such as in electronics or automotive industries often involves collaborative efforts between engineers, material scientists, and manufacturers to achieve the desired specifications.
spring for wire
An intriguing development in the field is the incorporation of smart technologies into spring production. Advanced sensing and monitoring technology can now be integrated into spring designs, allowing real-time data collection and analysis. Such innovations enhance the spring's performance, facilitating predictive maintenance and improving the overall reliability of the machinery or device. This technological edge not only prolongs the lifespan of the products but also aligns with the increasing market demand for smart and connected devices.
Trustworthiness in spring purchasing is another essential facet. Knowing that a supplier adheres to stringent international quality standards offers peace of mind. ISO certifications and other accreditations provide a benchmark for quality assurance, ensuring that springs meet the highest industry standards. Manufacturers who invest in rigorous testing and quality control protocols demonstrate their commitment to reliability, an aspect that greatly influences customer trust and loyalty.
Authoritativeness in this field is achieved through continuous innovation and adaptation to new technologies and materials. Leading manufacturers often have dedicated R&D departments focused on developing advanced spring solutions that cater to emerging market needs. Engaging in partnerships with research institutions or participating in industry consortia can enhance a manufacturer’s reputation as a pioneer in spring technology.
Further, customer experience must be prioritized. This includes offering comprehensive support and services like custom design consultation, performance analysis, and after-sales support. Effective communication and responsiveness to queries or issues also play a vital role in establishing and maintaining strong customer relationships, thus promoting brand loyalty and reputation.
In conclusion, springs are not merely passive components in wire manufacturing; they are the dynamic elements that significantly impact the functionality and success of the final product. Capitalizing on advanced materials, precision manufacturing techniques, and smart technologies ensures that these critical components continue to meet the evolving needs of the industry. As manufacturers seek to enhance their operations and product offerings, an in-depth understanding of spring technology will be pivotal in driving future innovations and maintaining a competitive edge in the global market.