Understanding PVC Coated GI Binding Wire A Comprehensive Overview
PVC Coated GI Binding Wire, a versatile and robust material, is widely utilized in various industries due to its exceptional durability and resistance to harsh environmental conditions. This article aims to delve into the intricacies of this product, exploring its composition, benefits, applications, and the significance it holds in modern construction and manufacturing.
GI, an abbreviation for Galvanized Iron, refers to steel wire that has been coated with a layer of zinc to provide protection against rust and corrosion. The addition of PVC (Polyvinyl Chloride) coating further enhances these properties, offering an extra layer of defense against weathering, UV radiation, and chemical exposure. The combination of these two materials results in a highly durable and flexible binding wire that is ideal for numerous applications.
The PVC coating on the GI wire is typically done through a process called electrostatic powder coating. Here, the wire is first cleaned and degreased before being immersed in a bath of molten zinc to create the galvanization. Once cooled, the wire is then coated with PVC particles that adhere to the zinc layer, forming a seamless and robust covering. This process not only improves the wire's aesthetics but also significantly increases its lifespan.
The benefits of PVC Coated GI Binding Wire are numerous. Firstly, its corrosion-resistant properties make it suitable for outdoor applications where exposure to moisture and humidity is high. Secondly, the PVC coating provides excellent insulation, making it a preferred choice for electrical grounding and wiring purposes Secondly, the PVC coating provides excellent insulation, making it a preferred choice for electrical grounding and wiring purposes
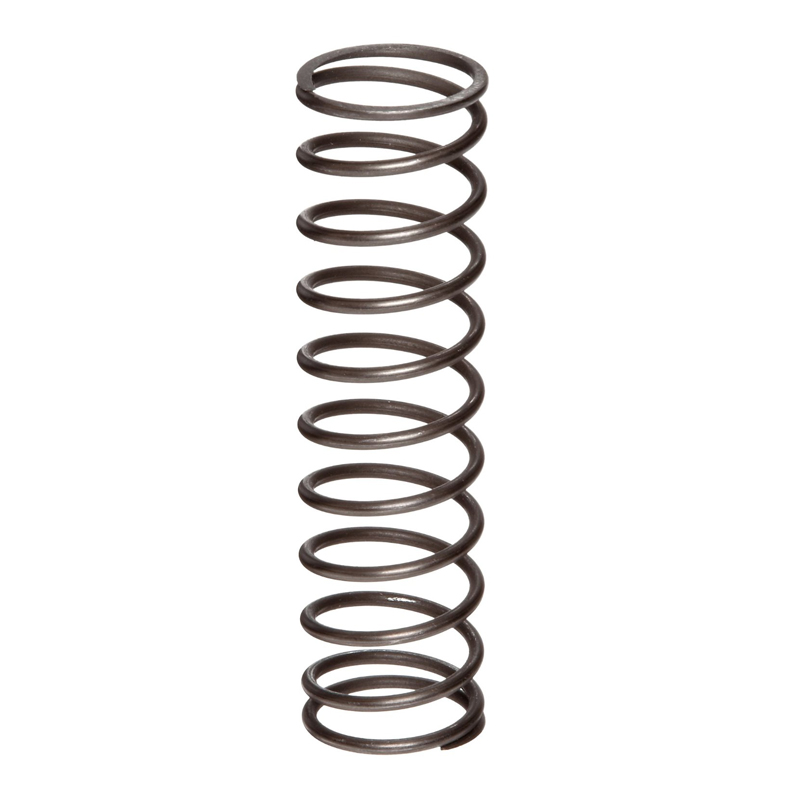
Secondly, the PVC coating provides excellent insulation, making it a preferred choice for electrical grounding and wiring purposes Secondly, the PVC coating provides excellent insulation, making it a preferred choice for electrical grounding and wiring purposes
pvc coated gi binding wire. Thirdly, its flexibility and tensile strength enable it to withstand mechanical stress without breaking, ensuring a secure and long-lasting bind.
In terms of applications, PVC Coated GI Binding Wire finds extensive use in construction projects, where it is employed for binding and reinforcing concrete structures. It is also commonly used in agriculture for securing fencing, trellising, and crop support. Furthermore, it plays a crucial role in the manufacturing of wire mesh, cable trays, and packaging materials. Its versatility extends to the electrical industry, where it serves as a reliable grounding wire.
The global demand for PVC Coated GI Binding Wire is continually rising, driven by its cost-effectiveness, ease of handling, and environmental friendliness compared to alternative materials. As sustainability becomes a key concern in various industries, the use of such coated wires, which have a longer life cycle and lower maintenance requirements, is likely to increase further.
In conclusion, PVC Coated GI Binding Wire is a testament to the marriage of functionality and innovation in material science. Its robustness, resilience, and adaptability make it a go-to solution across diverse sectors. With ongoing advancements in manufacturing processes, it is expected that this material will continue to evolve, meeting the ever-changing demands of the modern world.