Helical compression springs, often an unsung hero in the realm of mechanical innovations, are imperative in various applications ranging from everyday consumer products to complex industrial machinery. Understanding the nuances of these springs can provide insights into their pivotal roles, enhancing the decision-making process regarding their implementation in product design and repair.
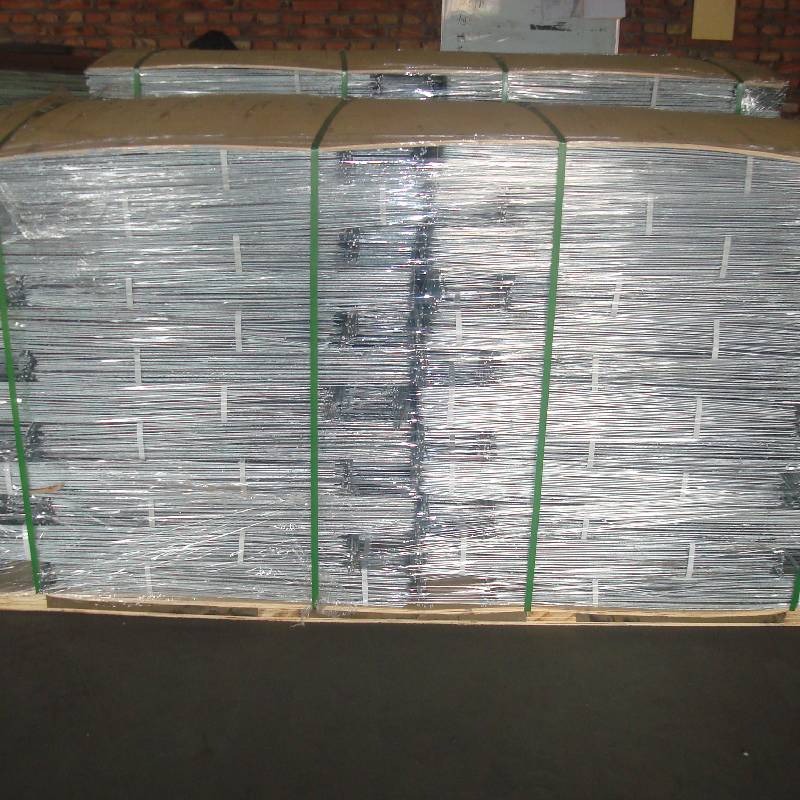
Being an expert in mechanical engineering, I've encountered numerous instances showcasing the efficiency of helical compression springs. Their primary function is to exert a resistive force when compressed, and they achieve this with unmatched precision due to their coiled structure. This seemingly simple coiling design imbues the spring with the flexibility to absorb significant amounts of kinetic energy, which is vital in both conserving and redirecting mechanical energy efficiently.
One striking feature of helical compression springs is their adaptability. Whether they are crafted from high-carbon steel for robust applications or from stainless steel to avoid corrosion in sterile environments, their material versatility is commendable. In sectors where weight savings are crucial, such as the aerospace industry, the use of titanium or specialized alloys can lessen the spring’s weight without compromising its strength or durability; a vivid testament to the expertise required in their manufacturing process.
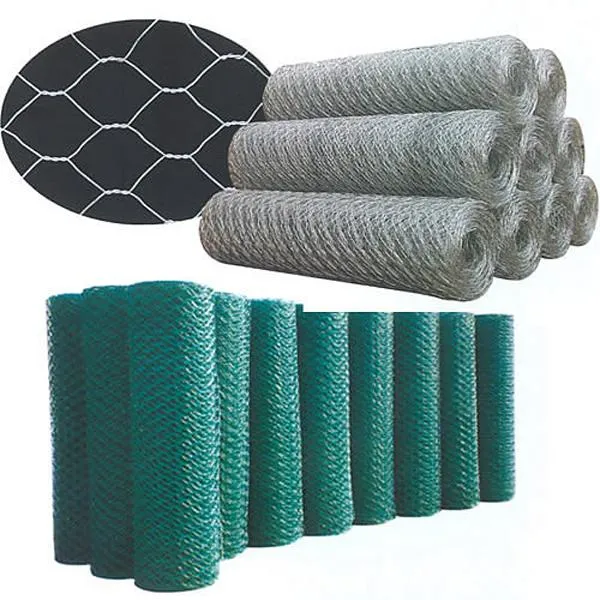
In my extensive experience, the rigor in choosing the ideal helical compression spring cannot be overstated. Factors such as the spring constant (K), wire diameter, coil diameter, and the number of active coils all play significant roles in the spring’s operational lifespan and performance. Thoroughly considering these parameters is essential in ensuring that the spring meets the specific requirements of its intended application.
helical compression
The reliability of helical compression springs is another area that underscores their authoritativeness. In automotive systems, for instance, they absorb shock from road irregularities, thereby enhancing vehicle comfort and prolonging the lifespan of the suspension system. Moreover, in electronic devices, these springs ensure the safe yet precise movement necessary for delicate operations, exemplifying their trustworthiness.
Advancements in computational tools have also made the customization of helical compression springs more precise. Simulation software allows engineers to predict the behavior under various stress conditions before actual production. This foresight prevents potential mechanical failures and enhances the safety measures for products incorporating these springs.
Lastly,
the eco-friendliness of these components cannot escape mention. With the growing emphasis on sustainable engineering practices, the recyclability of the materials used in helical compression springs positions them as an environmentally conscious choice. This sustainable aspect is increasingly becoming a critical factor as industries pivot towards greener solutions.
Overall, helical compression springs exemplify an intricate blend of simplicity in design and complexity in application. Their enduring presence across countless applications is a testament to their indispensable role in engineering. As industries continue to evolve, the strategic use of these springs will undeniably remain a cornerstone of innovation, affirming their place as a versatile and reliable component in modern technology.